利用有限元法预测夹具系统的工件变形
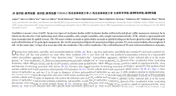
利用有限元法预测夹具系统的工件变形(中文1700字,英文1200字)
1. 介绍
分析装置的方法是必不可少的实践加工和经济学,尤其是能力模型。准确预测工件变形诱导夹具负载或预测未知的夹具工件。接触力是关键设计功能的装置。最常见的用于建模和分析方法。夹具 - 工件系统包括刚体方法,联系力学为基础的方法和有限元建模方法。这些建模方法[ 1-3 ]是无法通过的定义预测工件变形,因此不适宜夹具对零件质量的影响分析。 联系力学的方法,虽然从一个具有吸引力,计算努力的立场,零件可以是有限的,近似为弹性半空间。这种方法能够准确地预测未知,定位反应部队和本地化的接触变形[4 - 6]。然而,他们不适用兼容的零部件。另一方面,有限元模型是非常强大的,会计能为所有符合和非线性系统中存在。虽然利用有限元模型已beenwidely文献报道,受雇于在实践中,明确了不同的作用的认识.预测精度对工件的夹具符合变形是缺乏。也是知识的影响.不同的有限元模型参数对工件变形缺乏。
Prediction of workpiece deformation in a fixture system using the finite element method
1. Introduction
Methods for analyzing fixtures are essential to the practice and economics of machining. In particular, the ability to model and accurately predict workpiece deformation induced by fixturing loads and/or predict the unknown fixture–workpiece contact forces are crucial for designing functional fixtures. The most common modeling and analysis approaches used for fixture–workpiece systems include the rigid body approach, the [资料来源:http://Doc163.com]
contact mechanics based approach and the finite element modeling approach. Of these approaches, the rigid body modeling approach [1–3] is by definition incapable of predicting workpiece deformations and is therefore unsuitable for analysis of the impact of fixturing on part quality. The contact mechanics approach, although attractive from a
standpoint of computational effort, is limited to parts that can be approximated as elastic half-spaces. Models derived fromthis approach are capable of accurately predicting unknown locator reaction forces and localized contact deformations [4–6]. However, they are not applicable for thin, compliant parts. Finite element models on the other hand are very powerful and are capable of accounting for all compliances and nonlinearities present in the system. Although use of finite element models has been widely reported in the literature and employed in practice, a clear understanding of the role of the different fixture compliances on the prediction accuracy of workpiece deformation is lacking. Also knowledge of the effects of different finite element model parameters on workpiece deformation is lacking.