螺杆式压缩机
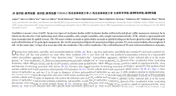
资料介绍:
螺杆式压缩机(中文5200字,英文3400字)
中文译文
1 引言
螺杆式压缩机是一种最常见的用来压缩气体的机器。它的结构简单,因为它基本上只包括一对互相啮合的螺旋形转子,它们包含在一个壳体中,紧密地配合在周围,转子和机壳之间有非常小的空隙。转子由外部的发动机和齿轮驱动,当转子旋转时,转子间的空隙以及转子与机壳之间的空间逐渐缩小。因此,在这种情况下,里面的气体就被压缩了。这种机器的几何构造是复杂的,流动的气体被压缩分三个阶段。首先,通过启动时转子的旋转,气体通过机壳一端的进气口进入齿间。其次,随着旋转的继续,转子之间的空间不再与进气口联合,因此,里面的气体就被压缩。最后,进一步旋转之后,转子的另一端经过位于机壳另一端的第二个端口,通过这个端口气体被排出。整个过程在齿的持续啮合中重复着,形成了一个从低压到高压持续而脉动的气流。
这些机器主要用于建筑业、食品业、加工业、制药业以及在冶金工业和气动输送中需要的地方。它们也广泛地应用于制冷和空调系统中所用的制冷剂的压缩以及化学工业中烃气的压缩。在过去30年,它们之所以相对快速地被接受是由于相比其他类型的容积式机器,它们拥有相对高的转速,这使得他们更加紧凑,它们能够在大范围的运作压力下保持高效率、高流速并且使用寿命长,依赖性强。因此,螺杆式压缩机在当前出售和使用的容积式压缩机中占有很大比例。
[资料来源:www.doc163.com]
螺杆式压缩机成功的主要原因归功于新型转子,它已大大减少了内部漏泄,以及先进的机床,它能以一个可接受的成本制造出最复杂的形状到3微米的公差。转子齿形的改善仍是最有前景的手段来更好地改进螺杆式压缩机。合理的程序正被研发,不仅用来代替早期经验得出的形状,而且能多样化地协调已选的轮廓,获得最佳的应用程序的压缩机必需的。尽管螺杆式压缩机大范围使用,但是由于它们内部构造的复杂性以及工序本身的不稳定性,直到现在,只有近似的分析方法能来预测它们的表现。因此,虽然众所周知,它们的单体被重物所施加的压力以及被自身的温度变化所扭曲,目前没法能精确预测这些扭曲的程度,也不能预测它们如何影响机器的总性能。另外,机器内部优化的流型模式有助更好的排气口设计。而且,更精确的测定轴承负载和它们波动的方式有助于更好的选择轴承。最后,由于压缩机自身温度和压力变化而导致转子和机壳扭曲,如果这个扭曲能被确实地预估,那么就能设计加工程序最大化地降低不利影响。
在螺杆机操作下的各种工作气体,其可以是与机器内的相位变化发生的气体,干蒸汽或多相混合物。他们可能会涉及驱油或其他液体注入过程中的压缩或膨胀过程中,没有任何形式的内部润滑。它们的几何形状可以依据每个转子上的齿,基本的转子轮廓和每个转齿片段上的相对部分来进行变化。因此没有通用的配置,适合各种应用程序的。因此,压缩过程详细的热力学分析和对各种性能设计参数的评估更能从这些机器上获得最好的结果,而非从能达到相同的用途的其他类型的机器上。所以,在优化程序主导下设计一套详细的标准是每个应用程序实现最好设计的前提。这样的指导方针,为进一步改善现有的螺杆机设计并扩大其广泛的用途也很重要。弗莱明等人在1998年对螺杆式压缩机的建模、设计和应用提供了一个很好的现代化评论。
[来源:http://Doc163.com]
热力学和流体流动过程的数学模型在这个专著中被提出,它在容积式机的螺杆压缩机和膨胀机的操作模式是有效的。专著中包括质量守恒定律公式的使用,包括运用于机器中的截面液即时控制卷的动力和能量,而这机器拨备液体渗漏、石油或其他流体注入、传热和实际流体参数。通过求解这些方程组,能获得机器中流体整体的吸收、释放、压缩或膨胀过程的压力容积图。
螺杆机的容量由转子轮廓而定,而转子轮廓根据普遍传动装置的使用以及气门的形状和大小。这个运算法则当解释明确时,能论证啮合条件,即能使多种转子的主要弧线通过分析或者离散点曲线得出。它的使用大大简化了设计,因为只有主要弧线需要被额定,而且这些能被设于主转子或闸转子或者其他任何包括齿条的拥有无限大半径的转子上。最有效的转子轮廓图已从一个联合转子架生成过程中得出。
转子轮廓形成处理器,热流体的解算器和优化器,连同预处理设施为输入数据和图形后处理和CAD接口,已被纳入一个设计工具,它以通过计算机编码的形式为分析和齿形优化以及其他几何和物理参数提供一个适当的工具。这个专著对比新的和传统的轮廓,概述了采用的基本原理和建模方法,并阐明了当应用于有油或者无油的空气压缩机和制冷螺杆式压缩机时,新的设计有潜在的改进方面。
[来源:http://Doc163.com]
专著的第一部分综述了螺旋式压缩机当前的发展。
英文原文
1 Introduction
The screw compressor is one of the most common types of machine used to compress gases. Its construction is simple in that it essentially comprises only a pair of meshing rotors, with helical grooves machined in them, contained in a casing, which fits closely round them. The rotors and casing are separated by very small clearances. The rotors are driven by an external motor and mesh like gears in such a manner that, as they rotate, the space formed between them and the casing is reduced progressively. Thus, any gas trapped in this case is compressed. The geometry of such machines is complex and the flow of the gas being compressed within them occurs in three stages. Firstly, gas enters between the lobes, through an inlet port at one end of the casing during the start of rotation. As rotation continues, the space between the rotors no longer lines up with the inlet port and the gas is trapped and thus compressed. Finally, after further rotation, the opposite ends of the rotors pass a second port at the other end of the casing, through which the gas is discharged. The whole process is repeated between successive pairs of lobes to create a continuous but pulsating flow of gas from low to high pressure. [资料来源:www.doc163.com]
These machines are mainly used for the supply of compressed air in the building industry, the food, process and pharmaceutical industries and, where required, in the metallurgical industry and for pneumatic transport.
They are also used extensively for compression of refrigerants in refrigeration and air conditioning systems and of hydrocarbon gases in the chemical industry. Their relatively rapid acceptance over the past thirty years is due to their relatively high rotational speeds compared to other types of positive displacement machine, which makes them compact, their ability to maintain high efficiencies over a wide range of operating pressures and flow rates and their long service life and high reliability. Consequently, they constitute a substantial percentage of all positive displacement compressors now sold and currently in operation.
The main reasons for this success are the development of novel rotor profiles, which have drastically reduced internal leakage, and advanced machine tools, which can manufacture the most complex shapes to tolerances of the order of 3 micrometers at an acceptable cost. Rotor profile enhancement is still the most promising means of further improving screw compressors and rational procedures are now being developed both to replace earlier empirically derived shapes and also to vary the proportions of the selected profile to obtain the best result for the application for which the compressor is required. Despite their wide usage, due to the complexity of their internal geometry and the non-steady nature of the processes within them, up till recently, only approximate analytical methods have been available to predict their performance. Thus, although it is known that their elements are distorted both by the heavy loads imposed by pressure induced forces and through temperature changes within them, no methods were available to predict the magnitude of these distortions accurately, nor how they affect the overall performance of the machine. In addition, improved modelling of flow patterns within the machine can lead to better porting design. Also, more accurate determination of bearing loads and how they fluctuate enable better choices of bearings to be made. Finally, if rotor and casing distortion, as a result of temperature and pressure changes within the compressor, can be estimated reliably, machining procedures can be devised to minimise their adverse effects. [资料来源:www.doc163.com]
Screw machines operate on a variety of working fluids, which may be gases, dry vapour or multi-phase mixtures with phase changes taking place within the machine. They may involve oil flooding, or other fluids injected during the compression or expansion process, or be without any form of internal lubrication. Their geometry may vary depending on the number of lobes in each rotor, the basic rotor profile and the relative proportions of each rotor lobe segment. It follows that there is no universal configuration which would be the best for all applications. Hence, detailed thermodynamic analysis of the compression process and evaluation of the influence of the various design parameters on performance is more important to obtain the best results from these machines than from other types which could be used for the same application. A set of well defined criteria governed by an optimisation procedure is therefore a prerequisite for achieving the best design for each application. Such guidelines are also essential for the further improvement of existing screw machine designs and broadening their range of uses. Fleming et al., 1998 gives a good contemporary review of screw compressor modelling, design and application.
[资料来源:http://www.doc163.com]
A mathematical model of the thermodynamic and fluid flow processes within positive displacement machines, which is valid for both the screw compressor and expander modes of operation, is presented in this Monograph. It includes the use of the equations of conservation of mass, momentum and energy applied to an instantaneous control volume of trapped fluid within the machine with allowance for fluid leakage, oil or other fluid injection, heat transfer and the assumption of real fluid properties. By simultaneous solution of these equations, pressure-volume diagrams may be derived of the entire admission, discharge and compression or expansion process within the machine. A screw machine is defined by the rotor profile which is here generated by use of a general gearing algorithm and the port shape and size. This algorithm demonstrates the meshing condition which, when solved explicitly, enables a variety of rotor primary arcs to be defined either analytically or by discrete point curves. Its use greatly simplifies the design since only primary arcs need to be specified and these can be located on either the main or gate rotor or even on any other rotor including a rack, which is a rotor of infinite radius. The most efficient profiles have been obtained from a combined rotor-rack generation procedure.
[资料来源:https://www.doc163.com]
The rotor profile generation processor, thermofluid solver and optimizer,together with pre-processing facilities for the input data and graphical post processing and CAD interface, have been incorporated into a design tool in the form of a general computer code which provides a suitable tool for analysis and optimization of the lobe profiles and other geometrical and physical parameters. The Monograph outlines the adopted rationale and method of modelling, compares the shapes of the new and conventional profiles and illustrates potential improvements achieved with the new design when applied to dry and oil-flooded air compressors as well as to refrigeration screw compressors.
The first part of the Monograph gives a review of recent developments in screw compressors. [资料来源:http://doc163.com]