套管注塑模设计(含工艺过程卡)
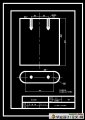
套管注塑模设计(含工艺过程卡)(含开题报告,中期检查表,论文说明书6800字,CAD图纸)
2.本课题的研究思路(包括要研究或解决的问题和拟采用的研究方法、手段(途径)及进度安排等):
1. 先通过收集和查阅各种文献资料和与同学老师的交流、指导,对目前国内外的塑料模具的发展状况和发展趋势进行深入的了解,预计用时五天;
2. 拿到工件的结构简图,对工件进行结构形状、尺寸精度、加工工艺性等方面作出详细地分析,并查阅相关资料看是否符合常规零件结构设计,预计用时三天;
3. 经过对塑件工艺性分析,拟订可行的工艺规程,并经过分析,研究,确定塑件注塑工艺参数并选择注射机的型号。估计用时间三天。
4.进行主要的设计计算,利用各种经验公式或者经验数据对塑件的质量和体积,型芯与型腔工作尺寸的计算,模具加热与冷却系统的计算以及注塑机有关参数的校核包括(注射量校核,模具厚度校核,开模行程校核,模具在注塑机上的安装与固定尺寸校核)预计需用时间四天;
5.根据塑件的结构,材料,生产批量来进行模具的总体设计,包括注塑机的型号选择,型腔数目的确定,型腔的排列方式,分型面的设计,导向方式,脱模方式的设计,浇注系统的设计等方面的设计;在设计中,应该综合考虑模具的安装,维修,生产效率等,预计用时间五天; [资料来源:http://www.doc163.com]
6. 对模具的主要零部件进行设计,主要有动模、定模、主流道、推件板、模架和导柱等零件,根据工作需要来设计尺寸,包括各零件的图纸,预计需用时间三天;
7. 模具的总装图和工作原理(有装配简图)需要用时间两天;
8. 模具主要零部件的加工工艺过程(凸模、凹模)分析与设计,预计用时间三天;
9. 模具的装配与调试,预计用时两天;
2 冲压工艺分析
此 工件只有落料和冲孔两个工序。但因为保证工件的加工精度来考虑,特做成级进模,所以要分步加工。由于每个工位都进行级进加工的话。其模架结构太大。此做成 四个工位的加工过程。即作成两个工位的级进复合模—落料冲孔加工。其材料是A3是旧代号,新材料代号是Q235。就有良好的冲压性能,具有变形量小的特 点,适应于冲裁加工。因考虑到工件相对尺寸较大和加工生产的效率的目的,便进行自动送料。模具的结构相对简单。只有直径90与28的落料和直径14.5与 50的冲孔。因工件是自由公差,因此孔采用IT12,落料采用IT14的公差标准。及完全满足普通冲裁的要求.
2.1 冲裁工艺方案分析和确定
该工件大体上包括落料和冲孔两个基本工序,可以采用以下几个加工方案:
方案一:先冲孔,再落料的基本加工工序,即采用一个一个的单工序级进模具加工。
方案二:冲孔—落料复合冲压一次,再采用单工序加工。即单工位复合加工。
方案三:冲孔—落料复合模具一次加工,完成工件加工。
方案四:冲孔—落料级进冲压加工,采用级进复合模具生产加工。
方 案一,模具结构相对简单,但是需要四个工位即要四套模具进行,而生产成本相对比较高的多且生产效率低,更难于大批量生产的要求。方案二,只要一套模具,工 件的精度及生产效率都非常的高。但模具的最大壁厚是(2.0~2.5)T,即易造成模具的强度较差,制造的难度也增加。而且冲压后,需要复合模具内部的废 料不容易排除来,对操作造成影响,即操作不方便。方案三,本方案也需要一套模具,工件也可以达到相当高的精度,生产效率也高。大是由于本模具需要划分多个 工位。造成模具的外形结构过大,模具成本增加,但不利于大批量生产。方案四,该方案也是一套模具。生产效率高,操作方便,工件精度也可以满足要求。通过以 上四个方案的分析,该工件利于第四个方案为佳。
3 主设计计算
3.1 排样方式的确定及其计算
[资料来源:www.doc163.com]
设计级进模具,首先要设计条料的排样图,因本工件是环形冲压垫圈。材料的利用率低,即要采用直排。如图所示:
搭边值根据工件的材料Q235和工件的厚度。选择其值为2.5㎜和2㎜,条料宽度为135㎜,步距是92㎜,一个步距的材料利用率是72.75%。查板材 标准,宜选择用950㎜×1500㎜的钢板。每张钢板可以剪成10张条料即95㎜×1500㎜。每张条料上可以有16个工位。故每张条料利用率是72%。
[来源:http://Doc163.com]
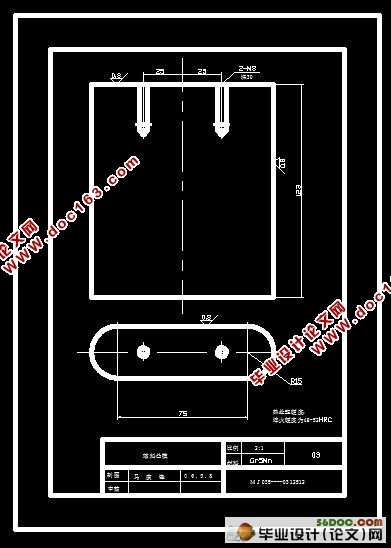
插图清单
排样方式的确定 …………………………………………….4
凹模形口图…………………………………………………..6
工件零件刃口…………………………………………………7
工件……………………………………………………………8
导正销…………………………………………………………2
[版权所有:http://DOC163.com]
顶料杆……………………………………………………….13
[来源:http://www.doc163.com]